-
Xingming Road, Yanyuan, Xingtan, Shunde, Foshan, Guangdong
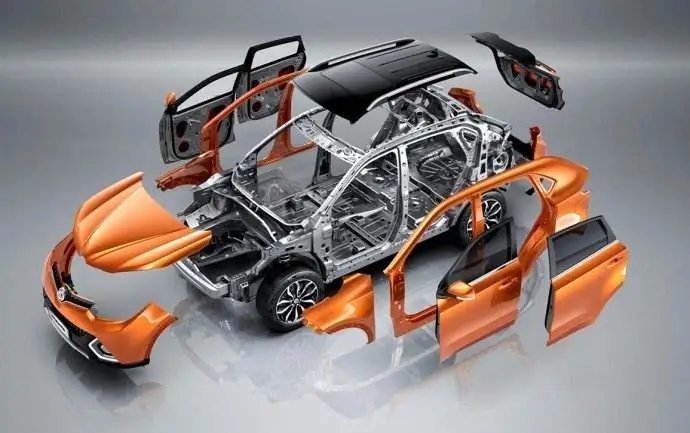
Auto Parts 2030: 6 Survival Rules in Electrification Era
The industry’s average EBIT margin has dropped to 4.7%, but Chinese suppliers are leading the way with a profit margin of 5.7%. The global parts battlefield is being divided into two new and old worlds by technology routes and geopolitics.
The global auto parts market is undergoing a deep reconstruction. Under the dual pressures of new energy transformation and geopolitics, the industry’s profit margin continues to be under pressure. Roland Berger research shows that the average EBIT margin of the parts industry has dropped to 4.7% in 2024, down 2 percentage points from before the epidemic.
At the same time, regional differentiation has intensified: Chinese suppliers lead Europe (3.6%) and South Korea (3.4%) with a profit margin of 5.7%, while North America accelerates localized production with tariff barriers, and Europe struggles with the dilemma of pure electric transformation not meeting expectations.
Based on the latest industry data, this article reveals six major trends, including electrification penetration rate lower than expected, regional supply chain reconstruction, lightweight material explosion, ceramic brake pad growth, aftermarket digitalization and compliance risk upgrade, providing strategic direction for parts companies.
1. Parallel electrification and hybrid technology: a dual-track strategy under the decline of pure electric vehicles
The growth of pure electric vehicles is encountering bottlenecks. Roland Berger predicts that the penetration rate of pure electric vehicles will drop to 41% in 2030, far lower than previously expected. The core resistance comes from the decline of EU subsidies and insufficient charging facilities, which has led to a reduction in the EU pure electric production forecast to 2.9 million vehicles in 2025.
Hybrid technology unexpectedly rebounded:
- China’s exports of plug-in hybrid vehicles surged 202% in the first quarter, driving demand for three-electric systems
- The power system cost of C-class pure electric vehicles is still 142% higher than that of fuel vehicles, and hybridization has become a compromise solution
- CATL’s semi-solid-state batteries are accelerating their landing, and it is expected to ship 10GWh in 2025, with a range of more than 1,500 kilometers
Power system suppliers are making up for the gap in pure electric sales through the rebound of hybrid components
2. Regionalization of supply chain reconstruction: near-shore production under tariff barriers
The dramatic changes in global trade policies are reshaping the manufacturing layout:
- The United States imposes a 25% tariff on imported light vehicles, prompting General Motors to launch a $4 billion domestic capacity expansion
- With the USMCA tariff advantage, Mexico’s exports of parts to the United States will increase by 32% in 2024
- The EU launched an anti-subsidy investigation on Chinese electric vehicles to accelerate the return of the supply chain
Chinese companies’ “technology + manufacturing” tiered strategy:
- Core components (such as aluminum motor housings) are fully automatically produced domestically
- Simple assembly links are transferred to Mexico/Southeast Asia
- Zhejiang Asia-Pacific Electromechanical cooperates with Russia’s Kamaz, and the technology transfer fee accounts for 20% of the contract amount
On average, Hyundai Motor contains 30,000 parts per car, one-third of which are plastic products – the tariff policy directly stimulates the demand for the local injection molding industry chain
3. Lightweight material explosion: a billion-dollar track spawned by new energy
Range anxiety drives material revolution: Every 10% weight reduction of electric vehicles can increase the range by 5%-8%. This makes magnesium alloy a new favorite:
- The global magnesium alloy automotive parts market will reach US$867 million in 2024 and will increase to US$1.294 billion in 2031 (CAGR 5.9%)
- China controls 80% of the raw magnesium production capacity, and companies such as Yunhai Metal have made breakthroughs in vacuum die-casting technology
- Wanfeng Aowei magnesium alloy instrument panel bracket has reduced weight by 36% and has entered BYD’s supply chain
Technological breakthroughs broaden application scenarios:
- Adding rare earth elements to improve corrosion resistance
- Honeycomb structure backplane reduces the weight of the braking system by 15%
- Carbon fiber composite commercial trucks reduce weight by 15% and increase fuel efficiency by 8%
Table: Comparison of lightweight material application effects | Τύπος υλικού | Weight reduction effect | Typical application parts | Cost premium | |————|————|—————-|————| | Magnesium alloy | 36% lighter than aluminum | Instrument panel bracket, steering wheel frame | 20-30% | | Ceramic brake pads | Wheel weight reduction of 8% | Braking system | 200-300% | | Carbon fiber composite materials | Vehicle weight reduction of 15% | Commercial vehicle body | 50-80% |
4. Ceramic brake pad market expansion: dual engines of high-end and environmental compliance
Increase in standard configuration rate of mid-to-high-end models:
- The global ceramic brake pad market will reach 23.94 billion yuan in 2024 and 29.34 billion yuan in 2031 (CAGR 3.0%)
- The sales share of luxury cars and SUVs will increase from 25% in 2019 to 35% in 2024
- The demand for new energy vehicles will increase by 5%, and stronger braking stability is required due to the increase in vehicle weight
Environmental regulations drive technology iteration:
- California AB 2289 requires copper content ≤5% in 2025
- Low copper formula uses graphene as a substitute, accounting for 30% of the European and American markets
- Bosch’s “low dust” product premium reaches 30-50%
The unit price of ceramic brake pads is 2-3 times that of semi-metallic brake pads, but the aftermarket penetration rate in China has soared from 10% to 25% in three years
5. Digital Revolution of Aftermarket Services: From Parts Sales to Ecosystem Construction
Profound Changes in Profit Structure:
- Changan Automobile Intelligent Driving Service Network User Payment Rate Reached 35%
- Shanghai Wanchao’s “Cloud Service Platform” Increased the Service Revenue from 5% to 18%
- CATL Battery Recycling System Nickel, Cobalt and Manganese Recycling Rate Exceeds 98%, Cost Reduction 40%
Model Innovation Breaks Through Growth Bottlenecks:
- The after-sales penetration rate of ceramic brake pads in Europe reached 45%, and the DIY culture in North America promoted e-commerce to account for more than 50%
- Zhejiang Gold built an auto parts platform, attracting 201 companies to settle in, with an assembly rate of 50%
- OTA upgrade services have become a new profit point, and OEM software spending will reach US$59 billion in 2030
6. Compliance and Geopolitical Risks: Survival Rules in the New Trade Era
Regulatory Barriers Continue to Rise:
- US FMVSS 305a requires compliance of battery electrolyte protection for light vehicles by 2027
- EU’s new battery regulations require a cobalt recycling rate of ≥16%
- Russia plans to impose a 15% tariff on imported parts
Technology decoupling risks intensify:
- The US intends to ban autonomous vehicles from using Chinese and Russian software and hardware
- China accelerates domestic substitution of automotive-grade chips
- EU REACH regulations restrict harmful substances in brake pads
Fuyao Glass’s smart dimming windows meet REACH standards, and its exports increased by 32.3% in the first eight months of 2024-compliance capabilities have become core competitiveness
Magnesium alloy parts are infiltrating the chassis of new energy vehicles, ceramic brake pads are quietly occupying high-end SUV original equipment, and in the newly emerging parts industrial park on the Mexican border, Chinese companies’ low-pressure casting machines are running 24 hours a day. These fragments together spell out the future picture: industry profit margins continue to be under pressure, but structural opportunities are clearly visible.
What Roland Berger calls the “stagnation and transformation period” is essentially a cruel reshuffle process. Three major fulcrums are needed to break the deadlock:
- Technology anchor: Betting on hybrid and pure electric dual-track technology, developing high-value-added products such as low-copper ceramic brake pads
- Regional deep cultivation: Promoting near-shore production in Europe and the United States, integrating new energy production capacity in Asia Pacific
- Efficiency revolution: Through AI production scheduling and standardized design, convert traditional business cash flow into electrification investment
The global parts battlefield has been split into multiple parallel universes. Only players who master both “Chinese costs” and “German precision” can pass the 2030 test.
FAQs:
Q1: Why is China’s auto parts profit higher than global average?
A: 5.7% EBIT margin via tech-led exports and cost control.
Q2: How will EV adoption impact suppliers by 2030?
A: Pure EV share drops to 41%, hybrid demand surges 202% YoY.
Q3: Where are suppliers relocating due to tariffs?
A: Mexico (32% export growth), Southeast Asia, and local US/EU hubs.
Q4: Which lightweight material grows fastest?
A: Magnesium alloys: $1.29B market by 2031 (5.9% CAGR).
Q5: Why are ceramic brake pads gaining share?
A: 5% EV demand spike + 30% premium for low-copper eco-designs.
Q6: What’s the #1 survival rule for auto suppliers?
A: Master hybrid tech + regional production + AI efficiency.