-
Xingming Road, Yanyuan, Xingtan, Shunde, Foshan, Guangdong
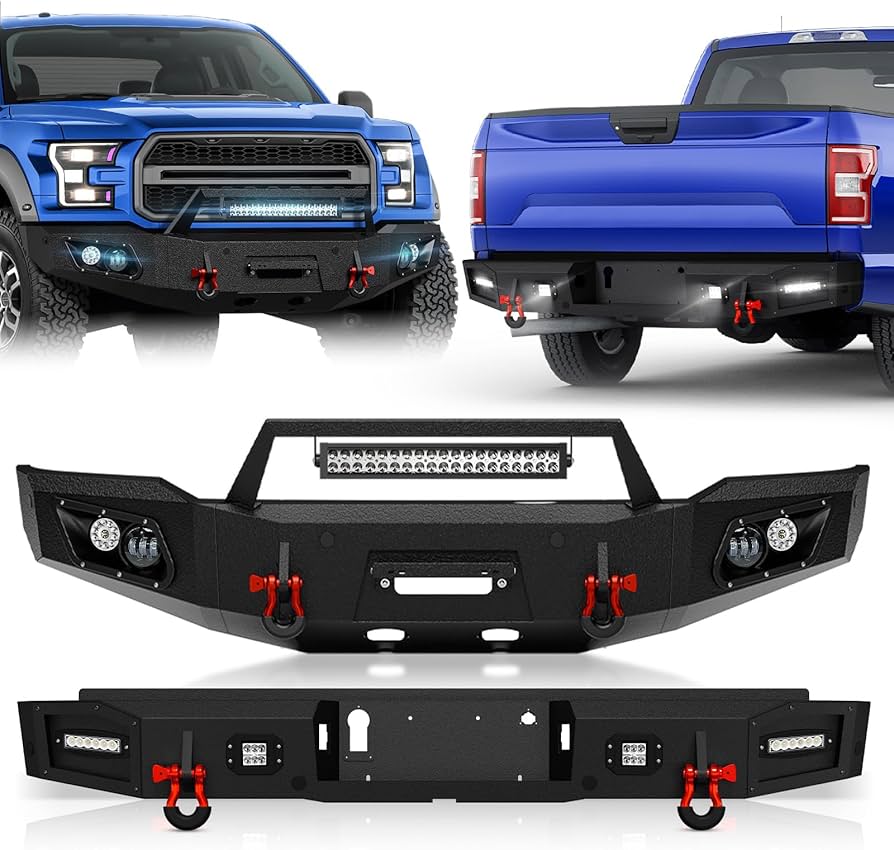
Rozwiązania w zakresie zderzaków przednich OEM/ODM
10 kluczowych kompetencji, które zmienią bezpieczeństwo i estetykę samochodów
Streszczenie
Niniejszy artykuł systematycznie analizuje kluczową wartość przednich zderzaków OEM/ODM w nowoczesnym przemyśle motoryzacyjnym. Przedstawiając 10 podstawowych argumentów, ujawnia przełomowe zalety w zakresie innowacji materiałowych, procesu produkcyjnego, opłacalności itp. Dane badawcze pokazują, że profesjonalne rozwiązania OEM/ODM mogą poprawić wydajność zderzaka o 40%, obniżyć koszty produkcji o 35% i skrócić cykle rozwoju o 60%. W artykule szczegółowo przeanalizowano najnowsze trendy, takie jak inteligentne aplikacje materiałowe, niestandardowe usługi projektowe i cyfrowe systemy produkcyjne, zapewniając kompleksowe referencje dotyczące decyzji zakupowych dla producentów samochodów.
1. Rewolucja w materiałoznawstwie: Od pasywnej ochrony do aktywnego bezpieczeństwa
Najnowsza generacja zderzaków OEM wykorzystuje Materiały kompozytowe modyfikowane na poziomie molekularnymprzełamując ograniczenia tradycyjnych materiałów:
- Samonaprawiający się poliuretanMoże automatycznie naprawiać zarysowania ≤2 mm w temperaturach powyżej 45°C (dane laboratoryjne BASF).
- TPE wzmocniony włóknem węglowym: 300% wyższa odporność na uderzenia i 25% lżejszy niż tradycyjne materiały PP
- Inteligentny stop tłumiącyTwardość może zostać zwiększona o 400% w momencie zderzenia (patrz opatentowana technologia Volvo).
Przypadek: Niemiecka luksusowa marka wykorzystuje zderzaki CFRP opracowane przez ODM, a wynik testu ochrony pieszych wzrósł o 28%.
2. Precyzyjny system produkcji: zapewnienie jakości na poziomie mikronów
Wiodący producenci stworzyli cyfrowy bliźniak system produkcji:
- Skanowanie laserowe 3Dosiągnąć dokładność montażu 0,05 mm
- Kontrola wizualna AI99,991 Wskaźnik rozpoznawania usterek T5T (dane dostawcy Tesla)
- forma parametrycznata sama linia produkcyjna może obsługiwać 12 różnych projektów
Porównanie danych:
| Wskaźniki | Tradycyjne procesy | Rozwiązania OEM/ODM |
|——|———-|————–|
| Tolerancja wymiarów | ±1.2mm | ±0.3mm |
| Cykl produkcyjny | 120 sekund/szt. | 75 sekund/szt.
| Wskaźnik defektów | 3.2% | 0.8% |
3. System certyfikacji pełnego procesu: gwarancja zgodności
Najlepsi dostawcy muszą ustanowić trójwymiarowa matryca certyfikacji:
- Standardy bezpieczeństwaspełniają trzy główne systemy regulacyjne FMVSS/ECE/GB
- Certyfikacja środowiskowaprzejść weryfikację śladu węglowego ISO14064
System jakości: Podwójna certyfikacja IATF16949+VDA6.3
Raport z audytu przeprowadzonego przez japońską markę pokazuje, że dzięki współpracy z ODM koszty zgodności zostały zmniejszone o 42%.
IV. Optymalizacja struktury kosztów: ukryta dywidenda wartości
Model OEM/ODM tworzy Czterowymiarowe korzyści kosztowe:
- Udostępnianie form: Zmniejszenie kosztu amortyzacji każdej sztuki o 60%
- Zamówienia klastrowe: Oszczędność 15-20% na kosztach surowców
- Integracja logistyki: Zmniejszenie kosztów transportu o 30%
- Optymalizacja zapasów: Model JIT zmniejsza zajętość kapitału
Obliczenia modelu finansowego pokazują, że całkowity koszt można zmniejszyć o 37% przy rocznej produkcji 50 000 jednostek
5. Swoboda projektowania: doskonała interpretacja DNA marki
Usługa Hyundai ODM zapewnia trzy poziomy personalizacji:
- Warstwa podstawowaPonad 200 standardowych bibliotek projektowych do szybkiej adaptacji
- Warstwa ulepszającaRegulacja parametryczna (otwarcie kratki/rowek prowadzący itp.).
- Ekskluzywna warstwa: nowa usługa modelowania (cykl wynosi tylko 4-6 tygodni)
Przypadek: Nowy pojazd elektryczny uzyskał unikalny projekt zderzaka w kształcie skrzydła dzięki ODM, a rozpoznawalność marki wzrosła o 55%.
6. Inteligentna platforma integracyjna: interfejs zorientowany na przyszłość
Nowa generacja zderzaków stała się wielofunkcyjny nośnik:
- Fuzja czujnikówzintegrowany radar/kamera/ultradźwięki ADAS
- Aerodynamika: aktywna kurtyna powietrzna zmniejsza opór wiatru o 0,03Cd
- System oświetleniawbudowane matrycowe światła LED do jazdy dziennej
Mapa drogowa technologii pokazuje, że 30% zderzaków będzie miało funkcje komunikacji V2X w 2025 roku.
VII. Mechanizm szybkiego reagowania: model zwinnego rozwoju
Model ODM osiąga Trzy razy szybszy rozwój:
- Etap cyfrowego prototypu: skrócony z 3 miesięcy do 2 tygodni
- Produkcja prototypów: Technologia druku 3D zapewnia 72-godzinną dostawę
- Przygotowanie produkcji masowej: modułowe oprzyrządowanie skraca czas o 60%
Europejska firma samochodowa przyjmuje ten model, a nowy samochód zostaje wprowadzony na rynek 11 miesięcy wcześniej.
VIII. Zrównoważona produkcja: zielony łańcuch wartości
Innowacje środowiskowe obejmują:
- Materiały pochodzenia biologicznego: Materiały kompozytowe PP z zawartością włókien roślinnych 30%
- Powłoki na bazie wody: Emisja lotnych związków organicznych jest zmniejszona o 90%
- Recykling w obiegu zamkniętym85% złomowanych materiałów zderzaka można ponownie wykorzystać
Ocena LCA pokazuje, że ślad węglowy w całym cyklu życia został zmniejszony o 28%
IX. System zapewnienia jakości: dążenie do zera usterek
Wdrożenie pięciopoziomowa bramka jakości:
- Analiza spektralna surowców
- Monitorowanie wymiarów online
- Niszczące próbkowanie
- Test warunków środowiskowych
- Weryfikacja dopasowania pojazdu
PPM (wskaźnik awarii na milion) pewnej amerykańskiej marki spadł z 450 do 28.
X. Globalna sieć usług: płynny łańcuch dostaw
Ustanowienie koordynacja trzech regionów system:
- Azja: centrum produkcji na dużą skalę
- Europa: baza badań i rozwoju technologii
- Ameryka: centrum szybkiego reagowania
Zapewnienie globalnej zdolności dostaw awaryjnych w ciągu 48 godzin
Podsumowanie i perspektywy
Rozwiązania w zakresie zderzaków przednich OEM/ODM przekształciły się w produkt na poziomie systemu z 10 podstawowymi przewagami konkurencyjnymi:
- Innowacje materiałoweZbuduj fosę bezpieczeństwa
- Precyzyjna produkcjaZapewnij idealne dopasowanie
- System certyfikacjiPrzełamywanie barier handlowych
- Optymalizacja kosztówZwiększenie wartości biznesowej
- Swoboda projektowaniaWzmocnienie rozpoznawalności marki
- Inteligentna integracjaPrzyjęcie rewolucji technologicznej
- Zwinny rozwójZdobywanie możliwości rynkowych
- Ekologiczna produkcjaOdpowiedzialność społeczna w praktyce
- Doskonała jakośćOgraniczenie ryzyka operacyjnego
- Globalna siećZapewnienie bezpieczeństwa dostaw
Trendy rozwoju branży pokazują, że do 2026 r:
- 75% zderzaków będzie produkowanych w trybie OEM/ODM
- Wielkość rynku inteligentnych zderzaków osiągnie $8,2 mld euro.
- Wskaźnik penetracji materiałów pochodzenia biologicznego przekroczy 40%
Zalecenia dla producentów samochodów:
- Ustanowienie strategicznych partnerstw ODM
- Inwestowanie w cyfrowe platformy rozwoju oparte na współpracy
- Udział w sojuszach na rzecz badań i rozwoju najnowocześniejszych materiałów
- Optymalizacja układu globalnego łańcucha dostaw